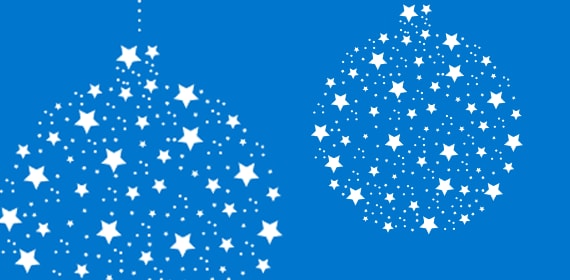
Season's Greetings!
Let us wish you a joyful, peaceful, and memorable holiday season. May it be filled with love, laughter, and cherished moments with loved ones. Happy Holidays!


AGA SMART PROPANE BOTTLE COMPOSITE 7.5 KG WITH HOUSEHOLD VALVE
A smart and snarky world first, the AGA smart propane bottle, is now available at selected locations. Matt black on the outside and smart on the inside: Built-in bluetooth and its own app give you full control over how much gas is left in the bottle.
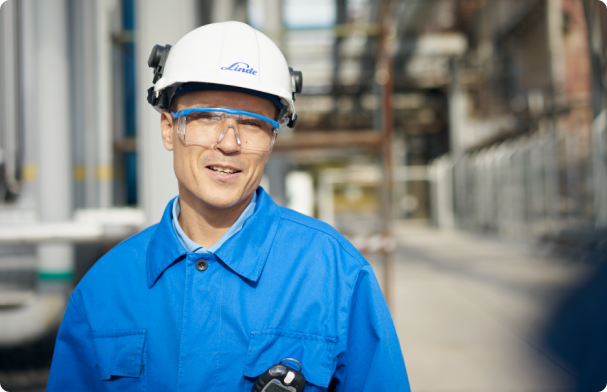
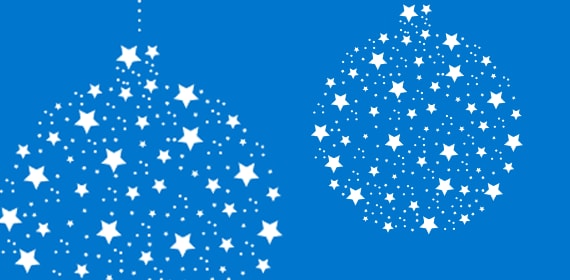
Season's Greetings!
Let us wish you a joyful, peaceful, and memorable holiday season. May it be filled with love, laughter, and cherished moments with loved ones. Happy Holidays!


AGA SMART PROPANE BOTTLE COMPOSITE 7.5 KG WITH HOUSEHOLD VALVE
A smart and snarky world first, the AGA smart propane bottle, is now available at selected locations. Matt black on the outside and smart on the inside: Built-in bluetooth and its own app give you full control over how much gas is left in the bottle.
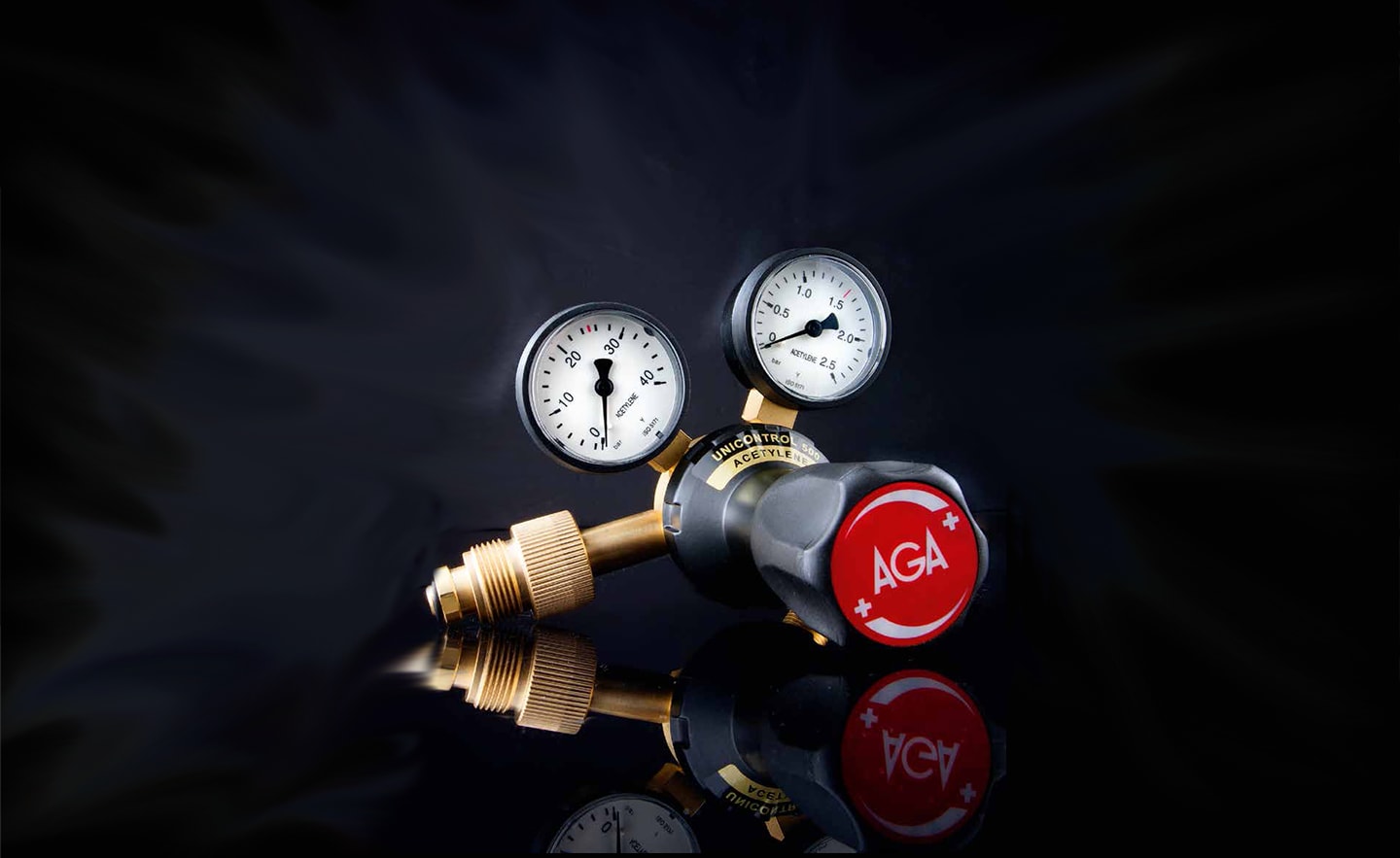
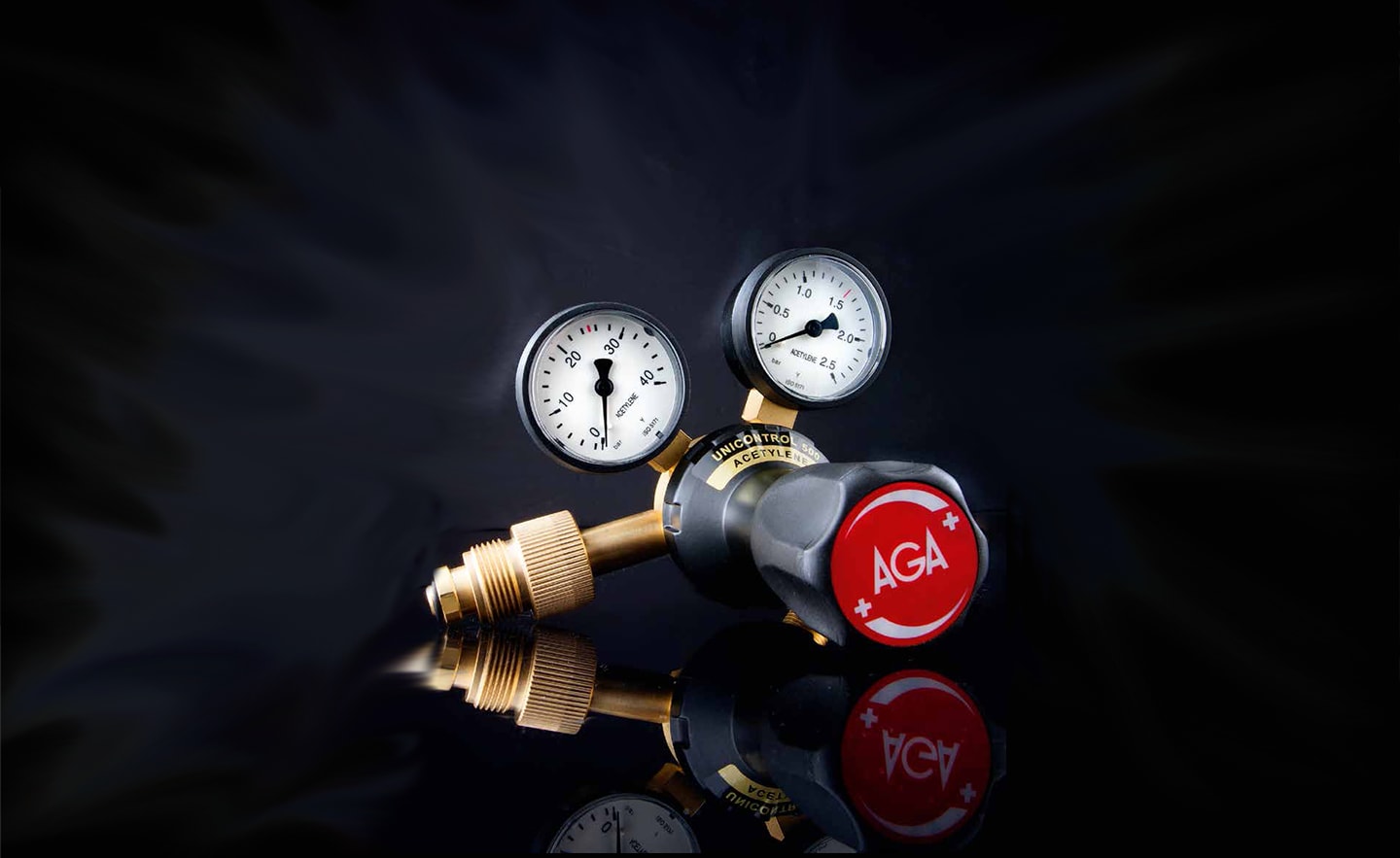
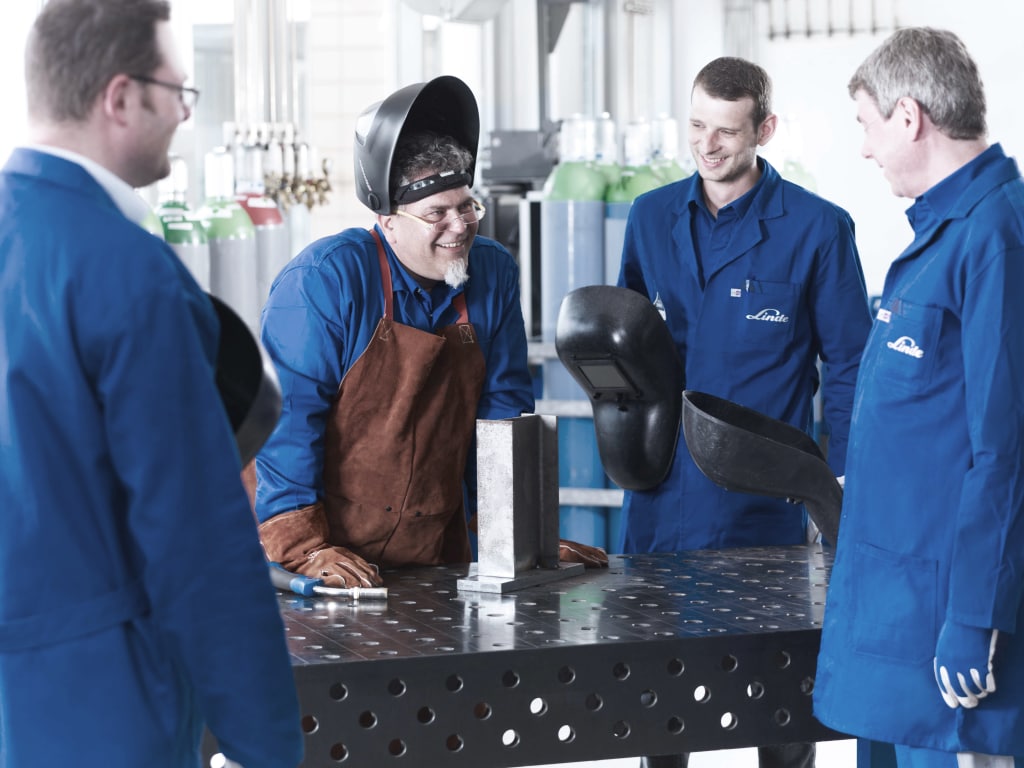
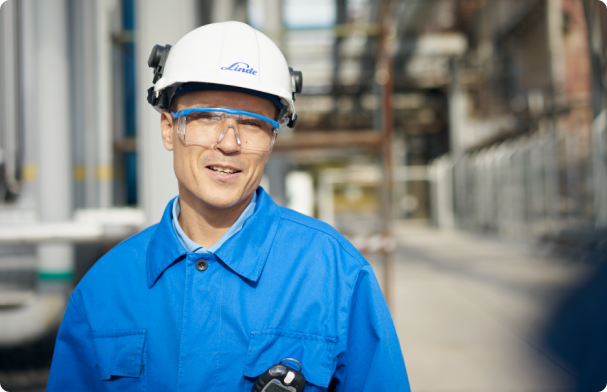